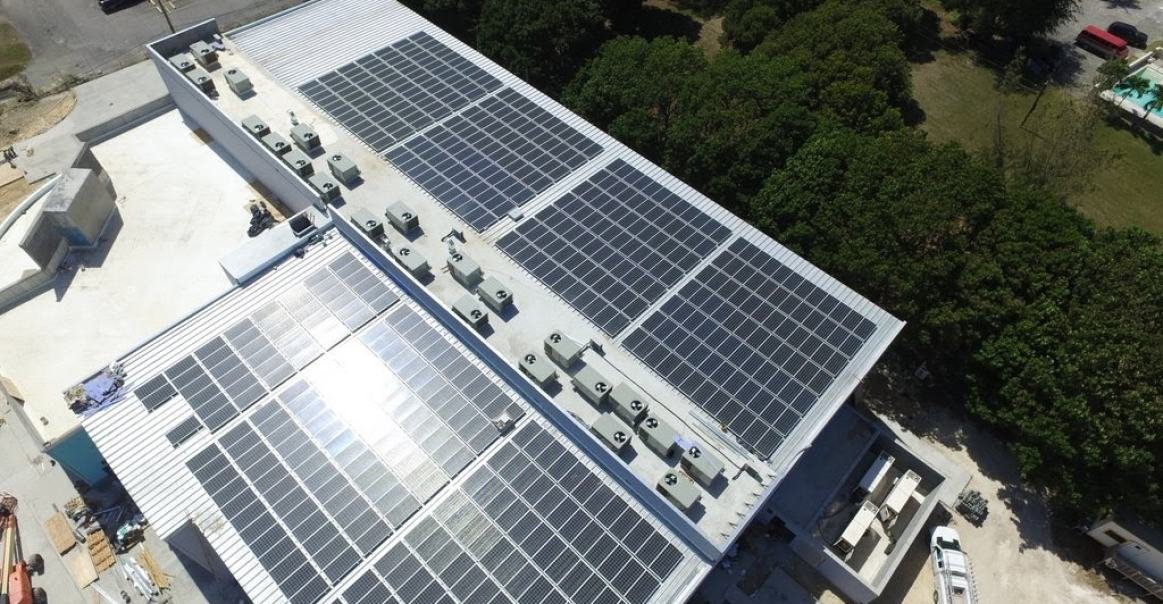
Half-Cell v. Full-Cell Solar Panels
In the past year or so many manufacturers have transitioned to half-cell solar panel production to increase power output (sometimes also called “Split Cell” technology). This means that commercial panels now have 144 cells instead of 72. Looking at the datasheets for Jinko’s 72 cell panel v. Jinko’s 144 cell panel the difference in the cell sizes is apparent.
A closer look at the spec sheets reveals a few more differences. The half-cell panels are slightly longer and the junction boxes have changed. With half-cell panels, the junction box is split in two, as you can see on the datasheet linked above and with the Q CELLS 144 cell panel as well.
Beyond the mechanical differences, there are some key electrical changes with the ways these 144 cell panels are wired. This article from Energy Sage offers a great diagram of each wiring scheme: in a full-cell panel the 72 cells are usually wired in 3 circuits and in a half-cell panel there are 6 circuits of cells.
Among other benefits, this wiring scheme yields a higher shade tolerance. In a full-cell panel if one cell is shaded the entire panel is affected, but if one cell in a half-cell panel is shaded only half the panel is affected. JinkoSolar’s white paper on bifacial technology goes into more detail on page 3:
“When installed vertically, half-cell technology can effectively cut down the shading loss. In half-cell module, there is parallel connection of the upper part and lower part. When 50% of the module surface is shaded like in the morning or evening, half-cell modules will still generate 50% of its nominal power while the power output of full-cell modules is 0”
Power output is higher with half-cell panels for a variety of reasons, one of which being that cutting each cell in half reduces the current within the panel which reduces resistive losses. This article from PV magazine and section 1.2 on page 3 of the JinkoSolar bifacial white paper dive into the details.
Bifacial Panels
There are two main types of bifacial modules in production: glass on glass panels and panels with transparent backsheets. “Glass on Glass” means there is a glass sheet on the backside of the panel in addition to the frontside, resulting in a heavier panel. A bifacial panel with a transparent backsheet is more similar to a monofacial panel, but with a backsheet that allows light to pass through. There are pros and cons to both bifacial options as discussed in this white paper from JinkoSolar and this article from PV magazine.
Q CELLS will have a half-cell glass on glass 405-watt panel available beginning in July 2020. This panel weighs 28.5kg. For comparison Q CELLS’ 400-watt monofacial panel weighs 23.5kg. Details on bifacial offerings from Q cells and production expectations can be found in this whitepaper.
Transparent backsheet bifacial modules are a good fit for projects that require a lighter panel. JinkoSolar offers such a panel- their transparent backsheet bifacial panel weighs 23.3kg. From what we can see in the above JinkoSolar video, the light will also shine through around each cell.
To read more about the production benefits of bifacial panels in different applications and guidance on spec’ing inverters, JinkoSolar and Q CELLS have both published white papers on bifacial solar panels.